ADAC
Learn how building an on-demand labor pool helped ADAC address demand volatility, respond instantly to demand, and build a layer of operational resilience
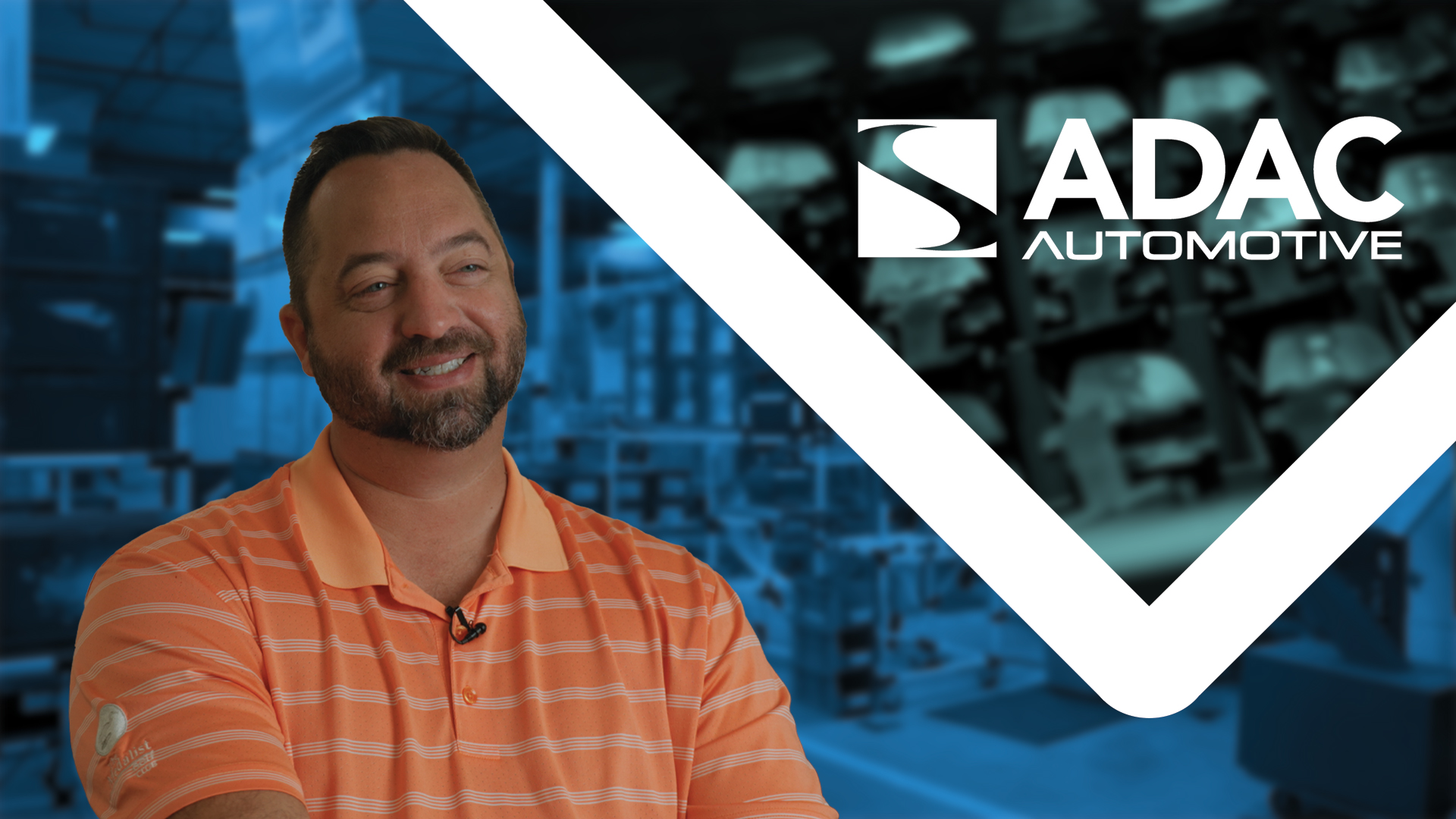
Weathering the Storm: ADAC Finds New Operational Speed and Resilience with Veryable
ADAC, a leading Tier 1 automotive parts supplier, serves major OEMs including Ford, General Motors, Stellantis, Honda, Nissan, Volkswagen, and BMW. Operating in one of the most demanding and unpredictable industries, ADAC has faced ongoing challenges with accurately forecasting and managing fluctuating labor demands. Weekly, monthly, and yearly staffing predictions were complicated by volatile order volumes and customer requirements, often resulting in costly overstaffing or missed deadlines due to understaffing.
To tackle this, ADAC turned to Veryable's on-demand labor platform to gain operational agility, optimize workforce management, and maintain its commitment to customers. Their partnership showcases how innovative labor strategies, supported by advanced technology, can drive operational excellence and business continuity in the automotive sector.
The Challenge: Navigating Labor Uncertainty in a Dynamic Industry
The automotive manufacturing landscape is complex and fast-changing, requiring suppliers to adapt quickly to evolving forecasts and fluctuating orders. As Jake Rupert, ADAC’s Head of HR, explains:
"It can be a challenge for us to understand what we need to staff this week versus three months from now. If we know we need an operator Monday, we can't afford to not have that operator on Friday, because that leads to excessive overtime or missed productivity. The long hours and variable shifts impact retention and morale."
Traditional labor models, which rely heavily on fixed staffing, did not provide the flexibility needed to respond to real-time shifts in demand. This unpredictability risked operational slowdowns, shipment delays, and ultimately customer dissatisfaction — outcomes that ADAC was determined to avoid.
The Solution: Building a Dynamic, Scalable Labor Pool with Veryable
ADAC leveraged Veryable’s on-demand labor platform to create a dynamic labor pool across three manufacturing plants and multiple work areas within just two months. This allowed the company to:
- Precisely schedule operators only when needed, significantly reducing unnecessary overtime and labor costs.
- Rapidly scale workforce capacity on short notice, sometimes with as little as three to four hours lead time, filling gaps during first, second, or third shifts.
- Engage a flexible talent pool including retirees, gig workers, and experienced manufacturing professionals who bring valuable institutional knowledge with minimal onboarding.
Jared McFarland, Team Lead at ADAC, notes:
"The transition has been smooth. Many of the operators we bring on through Veryable already have manufacturing experience or have worked here before, so integration and team cohesion are strong."
Additionally, the platform’s tagging and filtering capabilities allowed ADAC to quickly identify workers with specific skills or departmental experience, improving efficiency and ensuring that operators could hit the ground running with minimal training.
Operational Benefits: Meeting Customer Demand & Avoiding Burnout
The flexibility offered by Veryable enabled ADAC to better manage labor without overburdening full-time staff with excessive overtime. Jake Rupert highlights the workforce challenge:
"Every business’s biggest concern right now is workforce. It's not selling more products or finding new markets — it's getting the people to build the products and get them out the door. Veryable helps close that gap."
By meeting workforce needs precisely when they arose, ADAC maintained consistent production flow, avoided shipment delays, and improved employee satisfaction through more balanced scheduling.
Weathering the UAW Strike: Mitigating Disruptions & Cost Avoidance
The value of Veryable’s flexible labor model was dramatically demonstrated during the 7-week United Auto Workers (UAW) strike. ADAC was able to sustain operations by leveraging a highly skilled, repeat operator base sourced through Veryable, mitigating the strike's impact on production.
Once the strike ended and OEM demand resumed, ADAC scaled its workforce back up instantly — all at zero incremental cost. This agility helped ADAC avoid $400,000 in automation costs and achieve $1.6 million in total cost avoidance, as measured by the platform’s insightful performance metrics.
At ADAC’s May 2024 Partner Day Event, Veryable received the Innovation Award for its critical role in helping the company navigate these unprecedented challenges. To read more about this, click here.
Leveraging Data-Driven Insights for Continuous Improvement
Veryable’s platform not only provided workforce flexibility but also delivered actionable data insights. ADAC used performance metrics to track labor pool effectiveness, cost savings, and productivity improvements — enabling informed business decisions and demonstrating clear ROI on the partnership.
Jake Rupert shared: "Having baseline data helps me understand the impact of our investment, our savings, and how else we are providing value to the business."
Growth and Diversification: ADAC’s Expanding Horizons
Beyond automotive, ADAC is actively diversifying through a new business unit focused on leveraging their manufacturing, engineering, and quality expertise across multiple industries, including defense, medical devices, industrial automation, powersports, and agriculture.
Chris Teets, General Manager of the Diversified Business Unit, explains:
"ADAC’s unique capabilities allow us to be a full product lifecycle partner, providing design, engineering, and manufacturing services at a high level to new sectors."
President & CEO Jon Husby expects this diversified unit to represent 20% of ADAC’s revenue by 2028, highlighting the company’s growth ambitions bolstered by operational flexibility and quality execution.
Conclusion
ADAC’s partnership with Veryable has transformed how they manage labor — turning workforce unpredictability into a competitive advantage. By enabling just-in-time scalability, reducing overtime burnout, and maintaining production continuity through labor disruptions, ADAC continues to deliver world-class service to their automotive clients and beyond.
Manufacturers facing similar workforce challenges in automotive or other industries can look to ADAC’s experience as a compelling example of how on-demand labor can boost operational resilience and drive business success.
See Veryable for Yourself
Create a free business profile today to explore our platform.
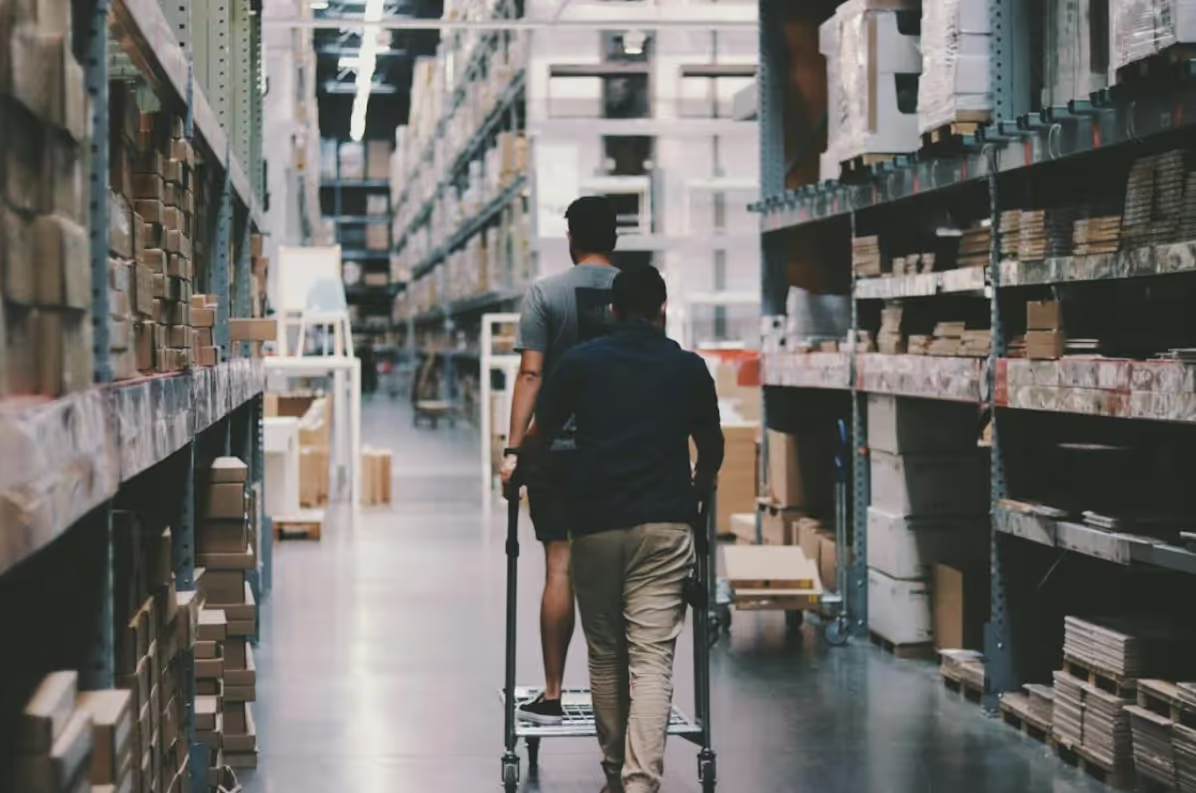