Metal Flow
Discover how precision metal stamping company Metal Flow has been able to 3x operational agility, accelerate quality inspections, and eliminate labor waste by building an on-demand labor pool.

Metal Flow Optimizes Quality Control Operations & Boosts Efficiency With On-Demand Labor
Metal Flow is a precision metal stamping company based in Holland, Michigan, known for producing complex airbag and fuel system components. With daily production volumes reaching up to a million parts for more than 40 customers across 14 countries, Metal Flow must consistently deliver uncompromising quality while navigating the highly cyclical nature of the automotive industry. Their demand patterns fluctuate dramatically based on customer schedules, which can change on a moment’s notice — a challenge that has historically made workforce planning difficult and expensive.
To address these fluctuations and ensure they could scale labor efficiently, Metal Flow turned to Veryable's on-demand labor platform. After meeting the Veryable team at a Lakeshore Advantage event, Metal Flow’s President Kelly Springer quickly recognized how a flexible labor model could help them stay nimble and responsive.
Gaining The Ability To Rightsize in Real-Time
For Metal Flow, responsiveness is key. Orders can spike overnight, new projects can launch with short lead times, or quality control inspections may need immediate resourcing. Veryable’s on-demand labor model empowed Metal Flow to build a flexible extension of their workforce, deployable at a moment’s notice.
“Using Veryable lets us flex our labor quite a bit,” explains Michael Hawkins, VP of Manufacturing. “With a flexible labor pool of about ten to fifteen percent, we’re able to adjust day by day, week by week. If we have a heavy workload off the presses or a heavy workload in quality, we can respond quickly. That flexibility and repeatability is almost like an extension of the team.”
Metal Flow’s supervisors can post available work (“ops”) as needed and invite proven operators from their trusted labor pool. These on-demand team members know the processes, understand the production flow, and are ready to jump in with little ramp-up time. Hawkins adds, “We’ve had some individuals that have been with us since we started with Veryable. They know where to go, what to do, what they’re looking for. It’s very important to build a relationship with them so they want to keep coming back.”
Accelerating Quality Control Inspections With Flexible Capacity
Maintaining quality is critical at Metal Flow, where defect rates must stay extremely low given the safety-critical nature of their parts. Automotive projects often have early launch requirements, such as EPC or GP12 processes, where parts must be sorted or inspected over a set period to validate production.
Veryable gives Metal Flow the capacity to handle these quality projects without pulling skilled full-time staff away from their regular duties. “Having the flexibility to bring people in to do those inspection criteria for a week to three weeks or even a couple months definitely helps,” Hawkins says. “We don’t have to take people off regular production of the parts to do inspections, which means our throughput stays consistent.”
In addition, the ability to build a repeatable, skilled pool of operators — backed by Veryable’s merit-based rating and review system — gives Metal Flow confidence that inspections and specialized tasks will be handled correctly the first time.
Optimizing Costs While Protecting Their Core Workforce
Beyond flexibility, Veryable has had a significant impact on Metal Flow’s cost structure. Carrying a large permanent workforce capable of handling spikes in demand led to excessive fixed cost exposure. Veryable’s model enabled Metal Flow to scale labor up or down daily, protecting their core team while avoiding unnecessary payroll expenses.
“Once you hire somebody, you’re carrying that cost,” says Ed Ploeg, Director of Quality. “From a labor standpoint, not over-hiring is what gives us our competitive edge. The key we learned with Veryable was once we developed our labor pool, we could pull from those people when we needed them, and we started realizing the value.
A Reliable Partner for Long-Term Success
Ultimately, Veryable has allowed Metal Flow to remain competitive in a demanding, rapidly changing industry. By flexing labor in near real time, Metal Flow can meet customer requirements, absorb unplanned shifts in production, and pursue new projects with confidence — without overburdening their core workforce or sacrificing quality.
As Hawkins reflects, “Orders drop in, and we’re able to respond quickly. That’s the key.”
With Veryable, Metal Flow has achieved an operational model that combines cost efficiency, high quality, and remarkable agility — laying the foundation for sustainable growth far into the future.
See Veryable for Yourself
Create a free business profile today to explore our platform.
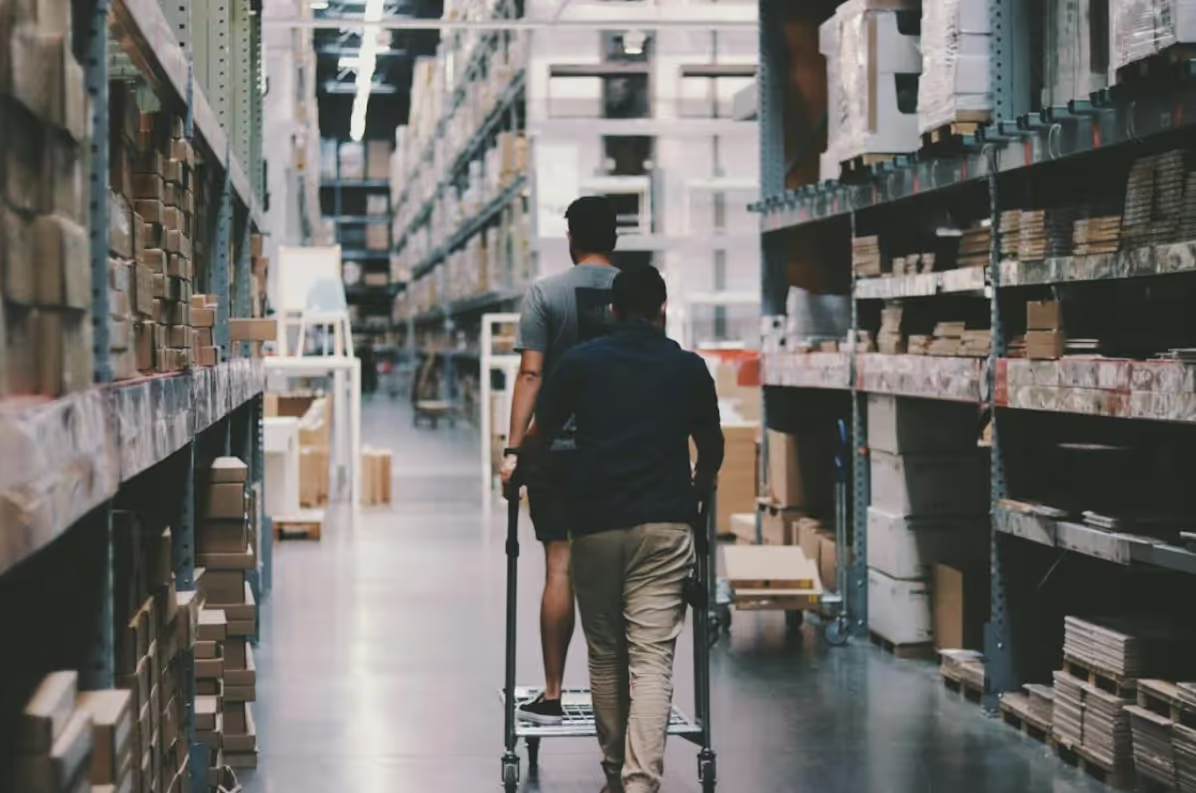