The Key to Optimizing Your Picking Productivity
In warehouse operations, the pickline is key to having efficient and reliable order picking productivity. Without a pickline, picking orders becomes a big consumer of labor hours and profitability. When walking through the warehouse operation, visual indicators of not having a pickline (or one that is not well maintained) are the proliferation of partial pallets throughout the storage area and people traveling back and forth across the facility while picking an order. Another indication is when outbound hours start to signifcantly accumulate above 50% of labor hours consumed.
Implementing a pickline can bring 15% labor reduction on the order picking function when designed and implemented correctly. The warehouse workers find the pickline beneficial as well due to the consistent flow of the pickline and building more stable shipments to prevent damage during transit.
The Pickline
To start on improving warehouse operations, pickline development begins with data analysis and pulling the past 12 months of sales data along with the item detail data. The item detail data is necessary to understand the case dimensions and weight to slot the pickline appropriately. A warehouse picker is going to be building a pallet or packing a box as they progress down the line.
Once you have cleansed data, the next step is to assign stack and movement classifications to sort the items into a manageable pickline. The stack classification will be driven by the item detail such as cube, weight, and case dimensions that will enable an order picker to build a stable shipment as its picked. The movement data then informs how many items to include and how to allocate the higher moving items throughout the pickline. Once movement slows down to less than a pick a day for an item, then the item does not have to be slotted into the pickline.
With all the analysis complete, the next step is to organize the pickline for slotting into warehouse operations. The pickline needs to start with the most dense items and then progress to the lower density items so not to crush the lower density items during shipping. A second pass through the items is required to make sure the high velocity items are dispersed enough throughout the pickline to avoid congestion but placed in the most accessible locations. To complete the slotting, a best practice is to add growth slots to accommodate new items – recommend adding 5% more positions.
Pickling Implementation
Now, it’s never the right time to slot a pickline into your operation or overhaul one given all the product handling required to pull it off. But with all the waste that not having it causes, the investment will be paid off in a short amount of time. A secondary benefit to warehouse operations is the task specialization that a pickline creates. A order picker will be expected to only pick and be assigned to a pallet jack while a dedicated replenisher keeps the pickline stocked on a lift truck. Implementing a pickline is a great first step to improve warehouse operations and gain an all important quick win to driving continuous improvement.
At Veryable, we’re here to help with a scalable, operational labor marketplace and assist with driving continuous performance improvement across the warehouse or fulfillment center.
To learn more, visit our homepage for continuous improvement, operational excellence, and Lean professionals.
Previous Posts
Trump 2.0 Week 23 In Review: Discussing A Potential July Deadline Extension, Negotiations With Key Trade Partners, & GE’s $490M Investment
The Future of Manufacturing and Logistics
Create a free business profile today to explore our platform.
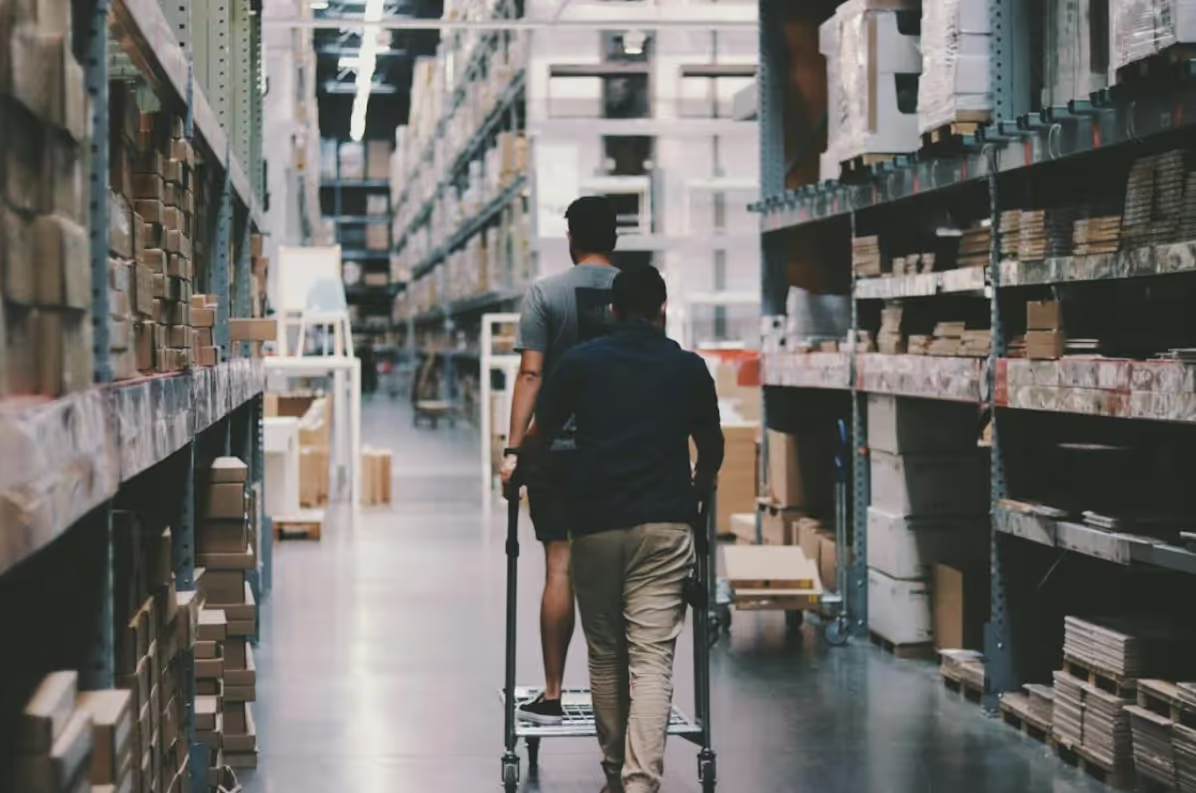